1. Exceeding the Working Load Limit (WLL): Perhaps the most critical mistake is overloading flat webbing slings beyond their rated WLL. Each sling is designed to handle a specific weight range, and exceeding this limit can lead to sling failure and potential accidents. Always check and adhere to the WLL specified by the manufacturer.
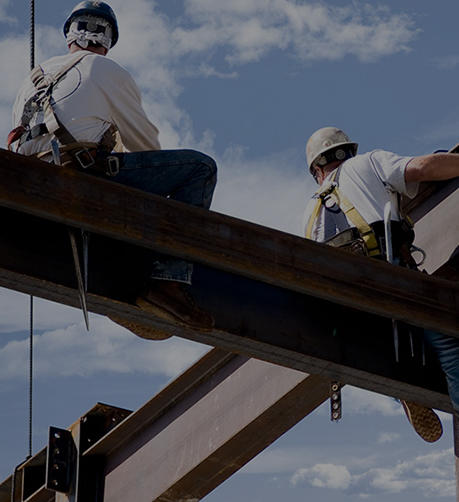
3. Inadequate Inspection: Regular inspection of flat webbing slings is essential to detect wear, damage, or defects that can compromise their strength. Inspect slings before each use and replace any sling showing signs of wear or damage to avoid accidents during lifting operations.
4. Lack of Edge Protection: When lifting sharp-edged or abrasive loads, failure to use appropriate edge protectors or padding can result in damage to the sling and potential failure under load. Always use edge protection to safeguard the sling and ensure safe lifting.
5. Twisting or Knotting: Twisting or knotting flat webbing slings during use can weaken the material and increase the risk of sling failure. Keep the sling flat and free from twists or knots to maintain its strength and integrity during lifting operations.
6. Improper Attachment: Using incorrect or insecure attachments, such as shackles or hooks, can compromise the safety of the lifting operation. Ensure that attachments are rated for the intended load and properly secured to prevent accidents.
7. Shock Loading: Avoid sudden or jerky movements during lifting, as this can create shock loads that exceed the WLL of the sling. Lift and lower loads in a controlled manner to minimize stress on the sling and prevent accidents.
8. Improper Storage: Improper storage of Flat webbing slings can lead to damage or degradation over time, reducing their strength and safety. Store slings in a clean, dry, and well-ventilated area, away from direct sunlight, chemicals, or sharp objects.