Webbing slings are designed to withstand demanding conditions and avoid fragmentation in complex environments due to several key features and design considerations:
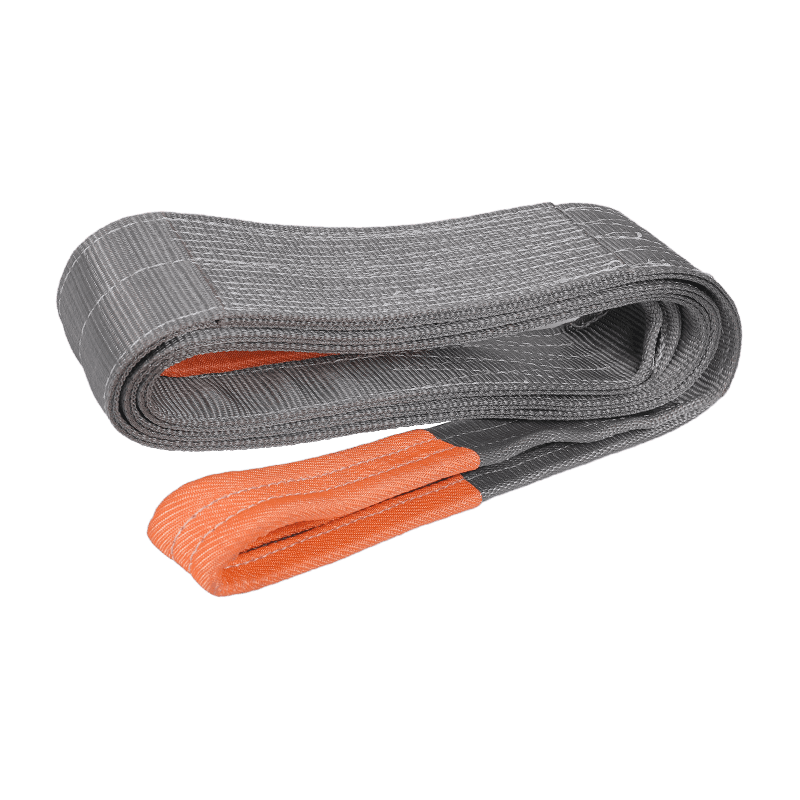
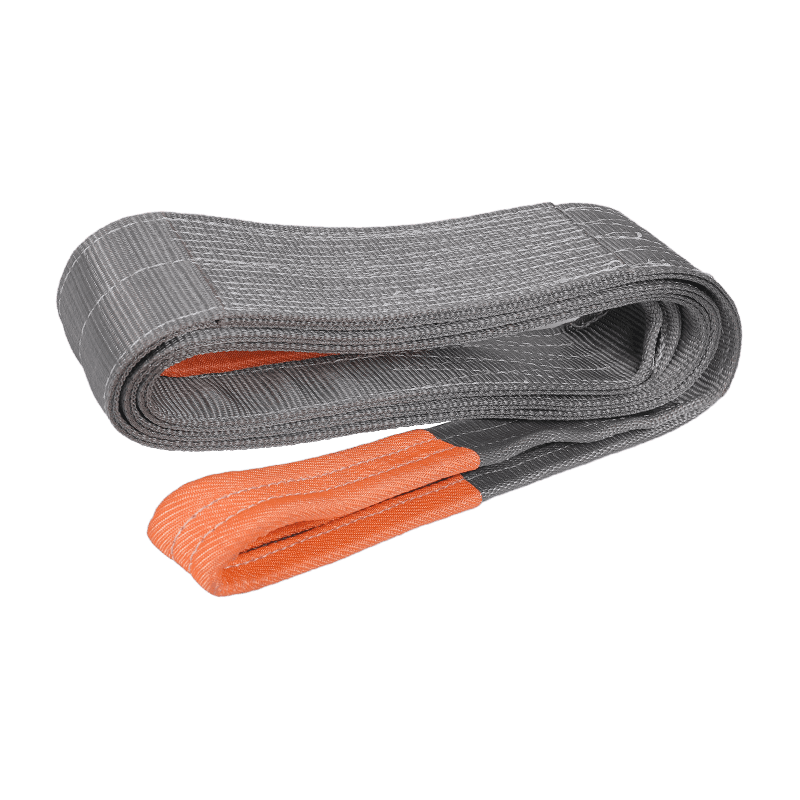
High-Quality Material: Webbing slings are typically made from strong and durable synthetic materials such as polyester, nylon, or polypropylene. These materials offer high tensile strength and resistance to tearing or breaking, even in challenging environments.
Multiple Layers and Reinforcement: Some webbing slings are designed with multiple layers of webbing or feature reinforced areas to increase their strength and resistance to abrasion. This reinforcement helps distribute the load more evenly and adds durability.
Edge Protection: Many slings incorporate edge protection features such as wear pads or reinforced sleeves to safeguard against fraying, cuts, or damage, particularly in areas prone to stress or abrasion.
Anti-Abrasion and Anti-Cut Coatings: Some slings have specialized coatings or treatments that offer additional protection against abrasion, cutting, or damage from sharp or abrasive loads.
Sturdy Stitching and Seams: The stitching and seams of Webbing slings are essential for their structural integrity. High-quality, reinforced stitching is crucial to prevent unraveling or splitting under stress.
Load Distribution: Webbing slings are designed to distribute the load evenly across their width. This feature helps prevent concentrated stress points that might lead to failure or fragmentation.
Compliance with Standards: Reputable manufacturers ensure that their webbing slings comply with industry safety standards and undergo rigorous quality checks during production to maintain their strength and durability.